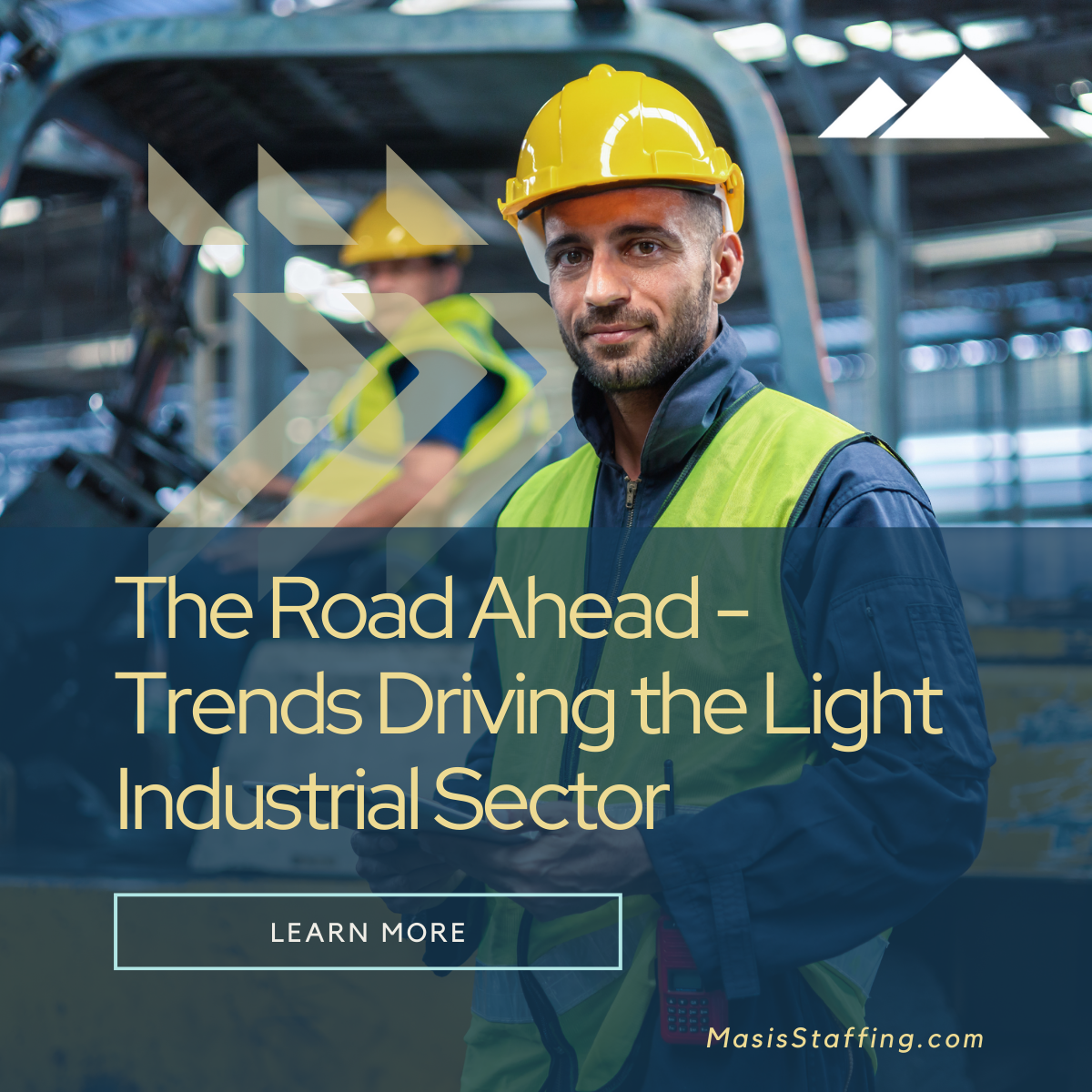
07 Feb Top Light Industrial Workforce Trends 2025
The light industrial sector, encompassing assembly, production, manufacturing, warehousing, and beyond, is a cornerstone of global industry. This area affects our everyday modern life and is continuously evolving, driven by advancements in technology, shifting workforce dynamics, and changing economic conditions.
It’s more critical than ever for businesses to stay ahead of trends to maintain efficiency, retain top talent, and navigate new challenges. We outline six key trends shaping the future of the light industrial sector and how companies can prepare for the year ahead.
-
Adoption of Advanced Automation Leading the Way
Automation remains a game-changer for light industrial operations. From robotic process automation (RPA) to artificial intelligence (AI)-powered systems, companies are investing in technology to streamline processes, minimize downtime, and fill labor gaps.
Why It Matters: Automation doesn’t just enhance productivity—it also addresses ongoing labor shortages, allowing businesses to operate more efficiently with fewer hands.
What to Watch in 2025: Collaborative robots, or “cobots,” are set to revolutionize operations by working alongside employees, enhancing both safety and flexibility. Deloitte’s 2025 Manufacturing Outlook confirms AI and automation are top priorities, with 50% of manufacturers planning to integrate these technologies into their workflows by 2026.1
Example of Application in a Manufacturing Environment:
Imagine a mid-sized electronics manufacturing company aiming to enhance efficiency and reduce defects in its production of circuit boards. By integrating Robotic Process Automation (RPA) and Artificial Intelligence (AI), the company could revolutionize its processes.
Deploy RPA for Repetitive Tasks
The company could begin by automating repetitive and precision-critical tasks on the assembly line. Robotic arms would handle precision soldering of components onto printed circuit boards (PCBs), eliminating inconsistencies caused by manual work. Automated systems could ensure accurate positioning of delicate components, reducing alignment errors. RPA-enabled robots could perform quick, automated checks for visible defects like missing or misaligned parts, ensuring baseline quality.
Leverage AI-Powered Systems for Quality Control and Smarter Production
To elevate their operations, the company could implement AI-driven to enhance quality control and optimize production workflows and supply chain management.
High-resolution cameras powered by AI could analyze each PCB in real time, identifying micro-defects or anomalies that might go unnoticed during manual inspections. AI models trained on historical production data could predict potential defects before they occur, allowing for proactive adjustments to minimize waste. Trained, predictive algorithms could monitor equipment, flagging early signs of wear or potential breakdowns, reducing costly unplanned downtime. Market trends and customer data could be analyzed to dynamically adjust production schedules, ensuring the company produces the right volume at the right time.
Combining RPA for repetitive tasks and AI for intelligent monitoring and analysis could enable this manufacturing company in reducing defects, improving efficiency, and maintaining high-quality standards.
-
Workforce Upskilling Becomes Essential
On the other hand, as automation takes on repetitive tasks, upskilling employees for higher-value roles will become critical. Employers should prioritize training in digital literacy, equipment maintenance, and advanced technical skills.
Why It Matters: Upskilling fosters a more adaptable workforce, reducing dependency on external talent while boosting employee retention. Implementing new systems, tools and automation will lead to demands for properly trained talent.
How to Adapt: Implement cross-training programs to teach employees diverse skills. According to PwC, upskilling workers not only improves productivity but also enhances job satisfaction, creating a resilient workforce equipped for the future.2 Consider how implementing a long-term and strategic workforce plan can help your organization get ahead of potential skill gaps.
-
Sustainability Takes Center Stage
In 2025, sustainability is no longer just a buzzword, it’s a keystone of operational strategy in the light industrial sector. As customers demand greener practices and governments tighten environmental regulations, companies are finding that eco-conscious initiatives are not only good for the planet but also beneficial for business.
Why It Matters:
Consumer Preferences Are Shifting – Studies show that a growing number of customers are prioritizing sustainability when making purchasing decisions. Eco-friendly businesses gain trust, loyalty, and a competitive edge in the market.
Regulatory Compliance Is Increasing – The National Association of Manufacturers (NAM), mentions stricter government regulations worldwide are requiring industries to meet ambitious carbon reduction goals, manage waste effectively, and adopt renewable energy solutions.
Financial Benefits – Sustainable practices often result in long-term cost savings by reducing energy consumption, minimizing waste, and improving efficiency throughout the production cycle.
How to Implement Sustainability Practices:
To remain competitive and compliant, light industrial companies can consider adopting the following sustainability strategies.
Circular Production Models – Circular production focuses on minimizing waste and maximizing resource efficiency by reusing materials, recycling components, and designing products for longevity. By rethinking production cycles, businesses can reduce raw material costs and decrease landfill contributions, benefiting both the environment and their bottom line.
Integration of Renewable Energy – Many companies are incorporating renewable energy sources, such as solar, wind, or hydroelectric power, into their operations. Renewable energy reduces dependence on fossil fuels, lowers utility costs, and positions businesses as leaders in green energy adoption.
Real-Time Sustainability Tracking – Using IoT (Internet of Things) and AI technologies, businesses can track energy usage, emissions, and waste in real-time. These systems provide actionable insights, enabling companies to adjust processes “on the fly” to meet sustainability goals. For example, tracking carbon output can help businesses identify inefficiencies and implement immediate corrections.
Sustainable Sourcing and Supply Chains – Partnering with suppliers who prioritize eco-friendly practices and reducing the transportation distance of materials to lower emissions. Localized and ethical sourcing enhances a company’s sustainability profile while reducing logistical costs and delays.
Employee and Community Engagement – Involving employees in sustainability efforts, such as energy-saving initiatives, waste reduction programs, or community green projects. Engaging the workforce builds a company culture centered around sustainability, enhancing employee satisfaction and public perception.
-
Flexible Staffing Models Address Labor Shortages
The sector continues to face labor shortages, particularly in skilled positions like machine operators and maintenance technicians. To combat this, companies are turning to flexible staffing solutions.
Why It Matters: Temporary and contract workers help fill gaps during peak seasons, while contingent workforce models provide agility in fluctuating markets. Temporary or temp-to-hire labor enables companies to cost-effectively scale when needed.
How to Adapt: Partnering with a staffing agency specializing in light industrial roles can provide access to a pool of skilled workers exactly when needed. Many firms will work directly with onsite supervisors and hiring managers, ensuring your individual requirements for hiring are still met.
-
Emphasis on Health and Safety Enhancements
Similar to increased sustainability efforts, there is increased awareness around worker safety, and wellbeing is driving investment in health and safety measures. From ergonomic workstations to AI-driven monitoring systems, businesses are prioritizing employee welfare.
Why It Matters: A safer work environment not only reduces downtime from accidents but also improves employee satisfaction and retention. Safety risks are increasingly becoming pain points and lead to climbing costs for manufacturing and production companies.
Key Trends: Wearable technology, such as sensors that monitor fatigue or posture, is gaining traction in light industrial settings.
-
Supply Chain Resilience and Localization are Paramount
Global disruptions in recent years have highlighted vulnerabilities in traditional supply chains. In response, companies are investing in local sourcing, digital tools, and predictive analytics to enhance supply chain resilience.
Why It Matters: A resilient supply chain reduces costs, shortens delivery times, and mitigates risks from global uncertainties.
How to Adapt: Develop relationships with local suppliers, implement AI for inventory management, and leverage government incentives for onshoring operations. The ManufacturingDive report3 emphasizes that a localized supply chain is key to navigating unpredictable markets.
Prepare for Success in 2025
The light industrial sector is evolving rapidly, and businesses that adapt to these trends will thrive in the face of change. From leveraging automation to investing in workforce upskilling and sustainability, the key to success lies in staying informed and prepared.
At Masis Staffing Solutions, we specialize in connecting businesses with the skilled talent they need to succeed in assembly, manufacturing, machine operation, and beyond. Let us help you prepare your workforce for the future.
Ready to get started? Contact us today!
- “2025 Manufacturing Industry Outlook”
https://www2.deloitte.com/us/en/insights/industry/manufacturing/manufacturing-industry-outlook.html
- “Manufacturers want to adopt generative AI. Where and how do they begin?”
https://www.pwc.com/us/en/industries/industrial-products/library/gen-ai-in-manufacturing.html
- “2025 Outlook: How U.S. manufacturers will face challenges and growth opportunities”